Understanding the Role of a Plastic Injection Mould Manufacturer in Metal Fabrication
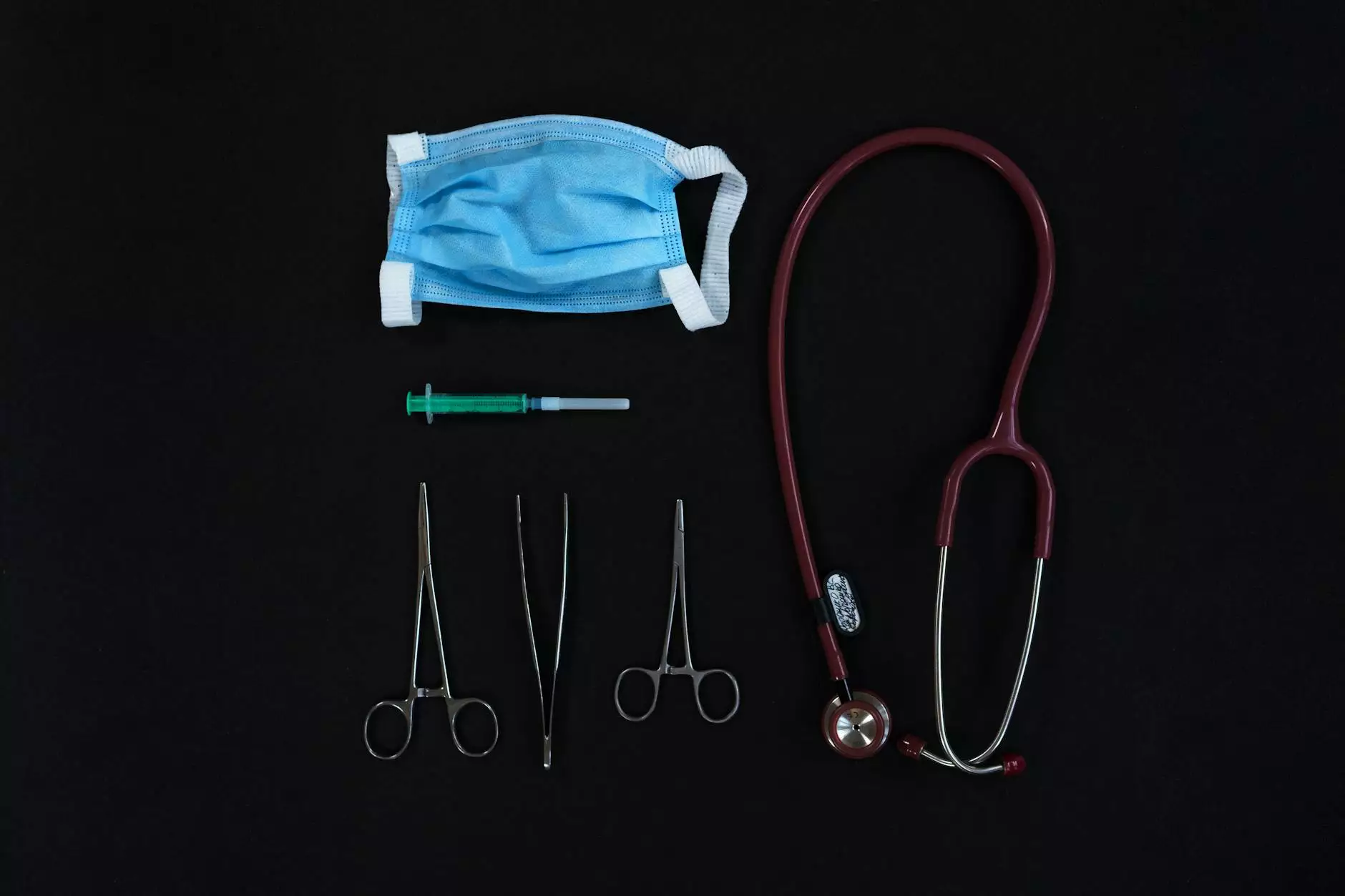
The landscape of modern manufacturing is intricate and multifaceted, with various elements working in harmony to create efficient production systems. Among these vital elements, the role of a plastic injection mould manufacturer stands out, particularly in the realm of metal fabricators. With the growing demand for precision-engineered components across different industries, understanding the nuances of plastic injection moulding becomes increasingly important.
What is Plastic Injection Moulding?
Plastic injection moulding is a manufacturing process that involves creating parts by injecting molten plastic into a mould. This process is renowned for its precision, efficiency, and ability to produce complex shapes. As a core technology used by a plastic injection mould manufacturer, it plays a fundamental role in various applications, from automotive components to consumer goods.
Key Steps in the Plastic Injection Moulding Process
- Designing the Mould: The first step involves creating a detailed design of the mould that will shape the final product. This includes considering the material properties and the end-use of the product.
- Material Selection: Choosing the right plastic material is critical. Factors like tensile strength, flexibility, and temperature resistance must be considered.
- Injection: The plastic is heated until it becomes molten, after which it is injected into the mould under high pressure.
- Cooling: Once the mould is filled, the plastic is allowed to cool and solidify, taking the shape of the mould.
- Demoulding: After cooling, the mould is opened to release the final product, which may require finishing processes.
Benefits of Working with a Plastic Injection Mould Manufacturer
Collaborating with a reputable plastic injection mould manufacturer provides numerous advantages to manufacturers and businesses looking to enhance their production efficiencies and product quality. Here are some key benefits:
1. Cost Efficiency
Utilizing injection moulding can drastically reduce costs due to its ability to produce parts at high volume. The initial investment in mould creation is offset by the reduced per-part manufacturing costs, making it an economically viable choice in the long run.
2. Design Flexibility
One of the standout features of plastic injection moulding is design versatility. Manufacturers can create intricate geometries and complex designs that would be challenging or impossible with other methods.
3. Consistency and Quality
The precision of the injection moulding process ensures that every part produced is consistent in quality and dimensions. This reliability is essential for industries such as automotive and medical, where precision is non-negotiable.
4. Minimal Waste
Injection moulding is one of the most efficient manufacturing techniques, producing minimal waste compared to traditional manufacturing methods. This efficiency aligns with sustainable practices, which many businesses are striving to implement.
Applications of Plastic Injection Moulding in Metal Fabrication
The synergy between plastic injection moulding and metal fabrication is evident in numerous applications across various sectors. Here are some notable examples:
1. Automotive Industry
In the automotive sector, a plastic injection mould manufacturer plays a crucial role in creating components such as dashboards, grille parts, and housings for electrical components. These parts must not only meet strict regulatory standards but also withstand harsh conditions.
2. Electronics
The consumer electronics industry relies heavily on plastic injection moulding for items such as casing for phones, laptops, and various appliances. The need for a lightweight yet strong material makes plastic an ideal choice.
3. Medical Devices
For medical devices, precision and safety are paramount. Components such as syringes, casings for machinery, and even internal parts require the detailed work provided by skilled plastic injection mould manufacturers.
Choosing the Right Plastic Injection Mould Manufacturer
Not all mould manufacturers are created equal. Selecting the right partner is vital for your production's success. Below are key factors to consider:
1. Experience and Expertise
Look for a manufacturer with extensive experience in plastic injection moulding and a solid understanding of your industry’s requirements. Their expertise can help streamline the design and production process.
2. Quality Certifications
Verify that the manufacturer holds necessary quality certifications such as ISO 9001. This indicates a commitment to maintaining high-quality standards throughout their processes.
3. State-of-the-Art Technology
Utilizing the latest technology can improve efficiency and ensure higher quality in the moulds produced. A forward-thinking manufacturer will invest in advanced machinery and techniques.
4. Customization Capabilities
Customization is essential for meeting specific project requirements. Ensure your chosen manufacturer is willing and able to accommodate unique designs and specifications.
The Future of Plastic Injection Moulding
As industries continue to evolve, so too does the technology and processes associated with plastic injection moulding. The future holds exciting prospects, including:
1. Sustainable Practices
With the rise of environmental consciousness, manufacturers are increasingly looking to adopt sustainable materials and methods. Expect advancements in biodegradable plastics and recycling processes to become more prevalent.
2. Smart Manufacturing
The integration of IoT (Internet of Things) within manufacturing processes is on the rise. This can lead to enhanced monitoring and quality control in real time, minimizing errors and improving efficiency.
3. Advanced Materials
Innovation in material science will lead to new types of plastics that are stronger, lighter, and more versatile, expanding the capabilities of plastic injection moulding even further.
Conclusion
In summary, a plastic injection mould manufacturer is an invaluable partner for any business in the metal fabrication industry. Their role is not only to produce high-quality moulds but also to enhance efficiency, ensure quality, and support innovation. As manufacturing technologies advance, staying informed and connected with a skilled supplier can make all the difference in navigating the dynamic market landscape.
For businesses looking to leverage the benefits of superior mould manufacturing, deepmould.net stands as a trustworthy ally in providing the expertise needed in the competitive arena of metal fabricators.