2205 Stainless Steel vs 316: An In-Depth Analysis for Your Business
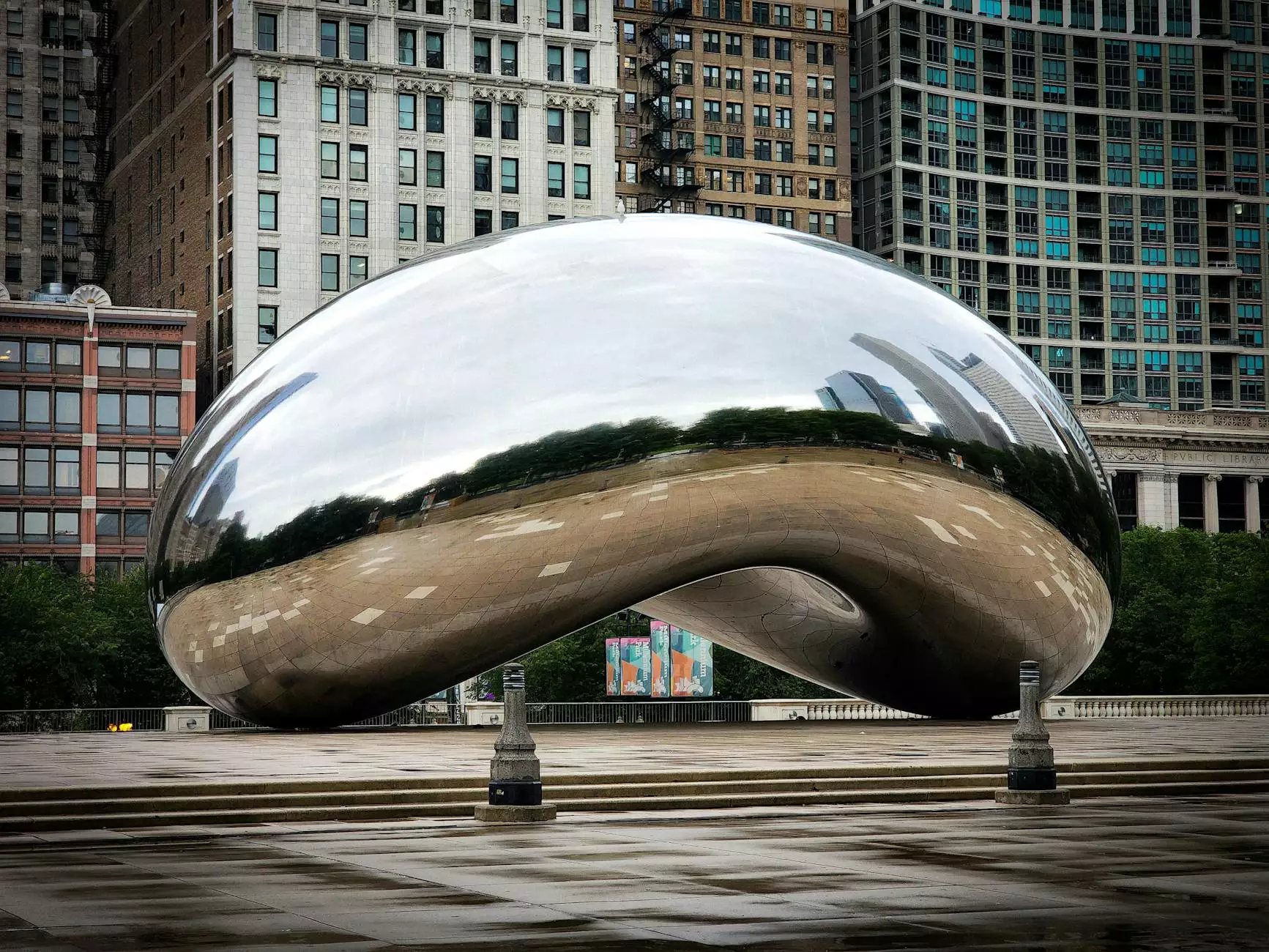
Stainless steel is a widely used material in various industries due to its durability, corrosion resistance, and aesthetic appeal. Among the many types of stainless steel available, 2205 stainless steel and 316 stainless steel are two that often come up in discussions surrounding material selection for business applications. This article delves into the key features, differences, advantages, and disadvantages of both materials, providing you with a comprehensive understanding to aid in your business decisions.
Understanding Stainless Steel Grades
Before we compare 2205 stainless steel and 316 stainless steel, it's essential to understand what these grades mean. Stainless steel grades are designated by the American Iron and Steel Institute (AISI) and are categorized based on their composition and properties. The two grades in question fall under the austenitic and duplex stainless steel categories.
What is 2205 Stainless Steel?
2205 stainless steel is a duplex (ferritic-austenitic) stainless steel alloy, which means it contains both austenite and ferrite microstructures. Its chemical composition includes:
- Up to 22% chromium
- 5-6% nickel
- 3-5% molybdenum
- 0.08% carbon maximum
- 0.20% nitrogen
This unique formulation gives 2205 its excellent mechanical properties and enhanced corrosion resistance, especially in chloride environments. It also has higher strength compared to traditional austenitic steels, making it suitable for demanding applications.
What is 316 Stainless Steel?
316 stainless steel, commonly referred to as marine-grade stainless steel, is another austenitic stainless steel. Its composition typically includes:
- 16% chromium
- 10% nickel
- 2% molybdenum
- 0.08% carbon maximum
The addition of molybdenum enhances 316 stainless steel's resistance to corrosion, particularly against chlorides and coastal environments, which is why it’s favored for marine and industrial applications.
Comparative Analysis: 2205 Stainless Steel vs 316
Corrosion Resistance
One of the primary concerns in material selection is corrosion resistance. Both 2205 and 316 stainless steels provide excellent resistance in a variety of environments; however, their performances can differ significantly in specific conditions.
2205 stainless steel excels in reducing pitting and crevice corrosion, particularly in chloride-laden environments. Its unique duplex structure allows it to withstand higher stresses in harsh conditions.
In contrast, while 316 stainless steel is marine-grade and performs well in saline environments, it may not perform as well as 2205 under severe conditions. In environments with high chloride concentrations, 316 can experience pitting, which can compromise the integrity of components over time.
Mechanical Properties
2205 stainless steel boasts higher yield strength—approximately double that of 316 stainless steel. For applications involving heavy loads or high stress, utilizing 2205 could result in lighter and more cost-effective designs. The mechanical properties of both grades are compared as follows:
- Yield Strength: 2205 (≥ 450 MPa) vs. 316 (≤ 220 MPa)
- Tensile Strength: 2205 (~620 MPa) vs. 316 (~580 MPa)
- Elongation (in 50 mm): 2205 (≥ 20%) vs. 316 (≥ 40%)
Weldability
Welding is a critical process in many manufacturing and construction projects. 316 stainless steel is known for its excellent weldability, making it an ideal choice for complex structures. On the other hand, while 2205 stainless steel can be welded, it requires specific techniques to avoid potential issues like embrittlement. It is advisable to use filler materials compatible with duplex steels when welding 2205 to maintain its corrosion resistance and strength.
Cost and Availability
When considering materials from a business perspective, cost and availability are crucial factors. Generally, 2205 stainless steel tends to be more expensive than 316 stainless steel due to its higher alloy content and newer technology involved in its production. However, the strength and long-term durability of 2205 can result in cost savings over time, particularly in applications where frequent replacement is necessary.
Applications of 2205 and 316 Stainless Steels
Common Applications for 2205 Stainless Steel
Due to its high strength and corrosion resistance, 2205 stainless steel is commonly used in:
- Oil and gas industry
- Chemical processing
- Marine applications
- Food processing
- Structural applications offshore
Common Applications for 316 Stainless Steel
316 stainless steel is widely utilized in:
- Marine environments (boat fittings, coast guards)
- Medical devices
- Pharmaceutical equipment
- Food and beverage processing
- Architectural features exposed to harsh weather
Why Choose the Right Material for Your Business?
Selecting the appropriate material for your business applications is not just about immediate costs; it entails considering long-term performance and reliability. By choosing the correct stainless steel grade, businesses can enhance product durability, minimize maintenance costs, and ultimately achieve greater customer satisfaction. Understanding the differences between 2205 stainless steel vs 316 allows companies to make informed decisions that align with their operational requirements.
Conclusion
In conclusion, both 2205 stainless steel and 316 stainless steel offer unique properties that suit different applications. When weighing your choices, it is essential to consider factors such as corrosion resistance, mechanical properties, weldability, and costs. While 2205 stainless steel may present initial higher costs, its strength and durability suggest long-term advantages, particularly in challenging regions. Conversely, 316 stainless steel remains a versatile option for less demanding conditions, especially in marine environments.
Ultimately, understanding these materials deeply can provide your business with the competitive edge needed for success. Deciding between 2205 stainless steel vs 316 should align with your specific application needs, budgetary constraints, and growth aspirations in industry sectors.